창고 재고 문제
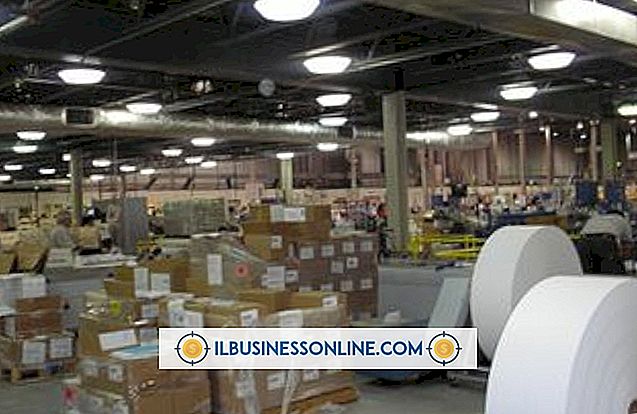
손상된 재고, 정확하지 않은 재고 실사 및 기타 재고 관련 문제가 모든 곳에서 발생합니다. 자전거 부품을 보유하고있는 중소기업에서 자동화 된 저장 및 검색 시스템을 갖춘 100 만 평방 피트 규모의 동급 시설에 이르기까지 다양합니다. 이러한 재고 문제의 근본 원인을 확인하는 것은 전체 프로세스를 줄이거 나 없애기위한 프로세스 개선 계획의 일부입니다.
부정확 한 수량
부정확성은 모든 창고가 직면 한 가장 큰 문제 중 하나입니다. 부정확 한 수량, 부정확 한 저장 위치, 부정확 한 가격 및 부정확 한 식별과 같은 여러 가지 형태의 부정확성이 발생합니다. 어느 시점에서 대부분의 회사는 창고에있는 하나 이상의 제품의 정확하지 않은 수량을 경험합니다. 이는 소매 업체, 특히 수백만 개의 제품 재고 보유 단위 또는 SKU가있는 대형 소매 업체의 경우 매우 자주 발생합니다. 종종 부정확 한 제품의 양은 다른 부정확 한 영역 중 하나에서 유래합니다. 웨어 하우스의 잘못된 위치에 배치 된 항목은 인벤토리를 검색 할 때 간과 될 수 있습니다. 이로 인해 인벤토리 항목이 부정확하게 계산됩니다.
생산 능력
크고 작은 창고의 경우 용량 문제는 종종 재고 문제와 동일합니다. 종종 창고에 팔레트와 인벤토리가 붐비는 경우 창고 관리를위한 기본 규칙이 간과됩니다. 재고를 더 많이 저장하려는 시도에서 제품은 종종 재고 관리 시스템에서 손상되고 분실되어 계산되지 않습니다. 스토리지 문제로 인해 오래된 재고 문제가 발생할 수도 있습니다. 회사는 하나의 제품 상자를 남겨 둘 수 있지만 저장 문제로 인해 찾을 수 없습니다. 그런 다음 제품은 쓸모 없게되고 회사의 대차 대조표에서 씁니다.
손해
재고는 일반적으로 창고에서 여러 번 처리됩니다. 접촉하거나 이동할 때마다 손상 될 수 있습니다. 많은 기업들이 상당한 손상을 입어 손상된 재고를 잃어 버리려고 노력합니다. 스크래치 및 파손 상품을 판매하는 가구 청산 센터에 대해 생각하십시오. 손상된 재고는 여러 가지 방법으로 발생합니다. 회사가 손상된 재고량이 많은 경우 문제의 원인을 판별하기 위해 근본 원인 분석을 수행하는 것과 동시에 추가 직원 교육을 고려해야합니다.
제품 식별
창고 재고 문제는 잘못된 레이블, 바코드, 제품 SKU 또는 포장으로 재고가 도착할 때 발생합니다. 예를 들어 주황색 플라스틱 컵에는 SKU가 ABC123이고 파란색 플라스틱 컵에는 SKU가 DEF456입니다. 두 컵 모두 카톤 당 100 개 단위로 포장됩니다. 각 상자의 외부에는 제품의 SKU 및 설명과 제품을 재고 소프트웨어로 스캔하기위한 바코드가 포함됩니다. 도착하자 마자 창고는 주황색 플라스틱 컵으로 표시된 바코드를 스캔하지만 제조사는 실수로 파란색 플라스틱 컵의 바코드를 상자에 넣었습니다. 창고 직원은 상자 내용을 확인하지 않고 바코드 스캔을 허용합니다. 이 행위는 즉각적인 재고 불일치를 초래합니다.
훈련
안타깝게도 많은 수의 창고 재고 문제는 부적절하거나 직원 교육의 부족으로 발생합니다. 일반적으로 재고 정확성, 손상 및 제품 식별과 관련된 문제는 사람의 실수로 추적 될 수 있습니다. 부적절한 훈련을받은 창고 직원은 숙련 된 인원이 정기적으로 피해야하는 재고 문제를 만듭니다. 예를 들어 자격 미달의 지게차 운전자는 숙련 된 지게차 운전자보다 재고 정리 및 회수 중에 제품을 손상시킬 가능성이 더 큽니다. 적절한 교육은 창고의 효율성과 생산성을 높이고 재고 관리 문제를 줄입니다.